A linear rail is a type of linear slide assembly with twin parallel tracks that contain balls or rollers that support the load. They provide low friction guidance and support for duties ranging from just a few grams to a few kilos. Their sizes, accuracy classes, and preloads make linear rails suitable for any performance. Using linear rails is endless, but there are some benefits over other types of guides according to the load capacity, travel accuracy, and rigidity. For instance, round shaft guides can withstand only downward or lifting loads, but linear rail guides can withstand moment loads and the other load lifting. Linear rails can go to long lengths which is useful as bulk material handling systems. When compared to plain bearing guides, direct have higher stiffness and great precision and control.
Single Rail Applications
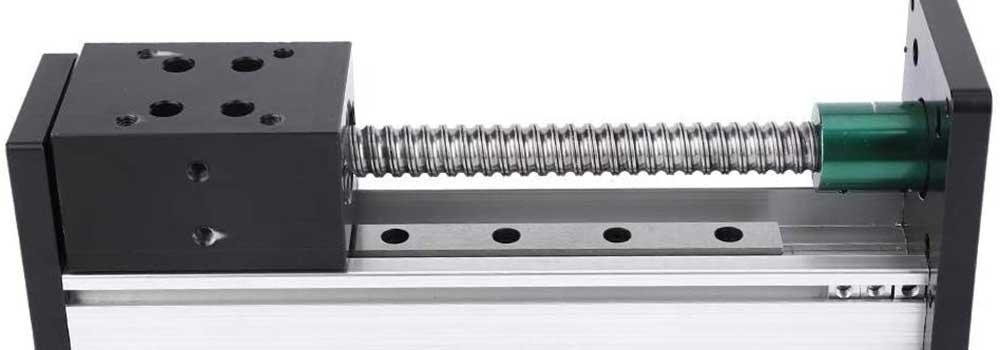
Linear rails have load-supporting rollers on each side of the rail so that they can withstand overhung loads even with a single rail. Because of these features, numerous applications use a single linear rail to save spaces. This also prevents issues with misalignment, among other rail components. Let’s take a look at a few examples of applications.
Linear actuators: Linear rails are often the guide mechanism of choice for actuators driven with belts, screws, etc. because of their ability to withstand moment loads. They can also provide travel speeds up to 5 m/sec, which is quite essential in belts.
Overhead transport systems: Loads are centered under the rail and the bearing. Rails like they are an excellent choice for guidance and support. The hanging transport system’s high load capacity allows heavy loads to be transported, and the rigidity of the linear rail helps to make the system stiff.
Dual Rail Applications
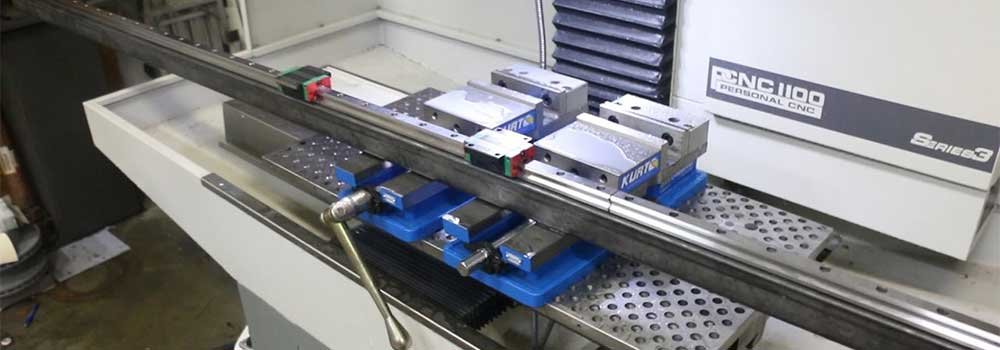
During high moment loads, linear rails can be used in pairs, allowing the load to be resolved into forces on the bearing blocks. In this arrangement, the drive mechanism can be mounted between the rails. Thus the system is made very compact. Dual rail applications consist of.
Linear stages: Stages are very high precision systems and can travel high accuracy. Even if the load is focused on the stage with no moment loading, dual linear rails are often used to ensure the stiffness, maximizing the bearing life.
Machine tools: Like stages, machine tools require very high levels of travel accuracy and stiffness, ensuring that the tool produces high-quality parts. Using two rails in parallel-typically with two bearing blocks per rail, this ensures the deflection is minimized.
Cartesian robots: Cartesian robots typically use one linear system per axis; that’s why it’s important that each axis can withstand high moment loads. Thus the cartesian robot axis is constructed from linear actuators that integrate two linear guides parallelly.
Robot transport units: Six-axis robots incorporate more flexibility for applications that need to be reached and rotated in many directions. But if the robot requires movement to another work area, then the dual-rail systems can act as an additional axis. The other axis can be called the seventh axis and can help transport the robot to a new location.
For applications that don’t need full load support, other linear guides like round shaft systems, plain bearing guides can be much more suitable and affordable.
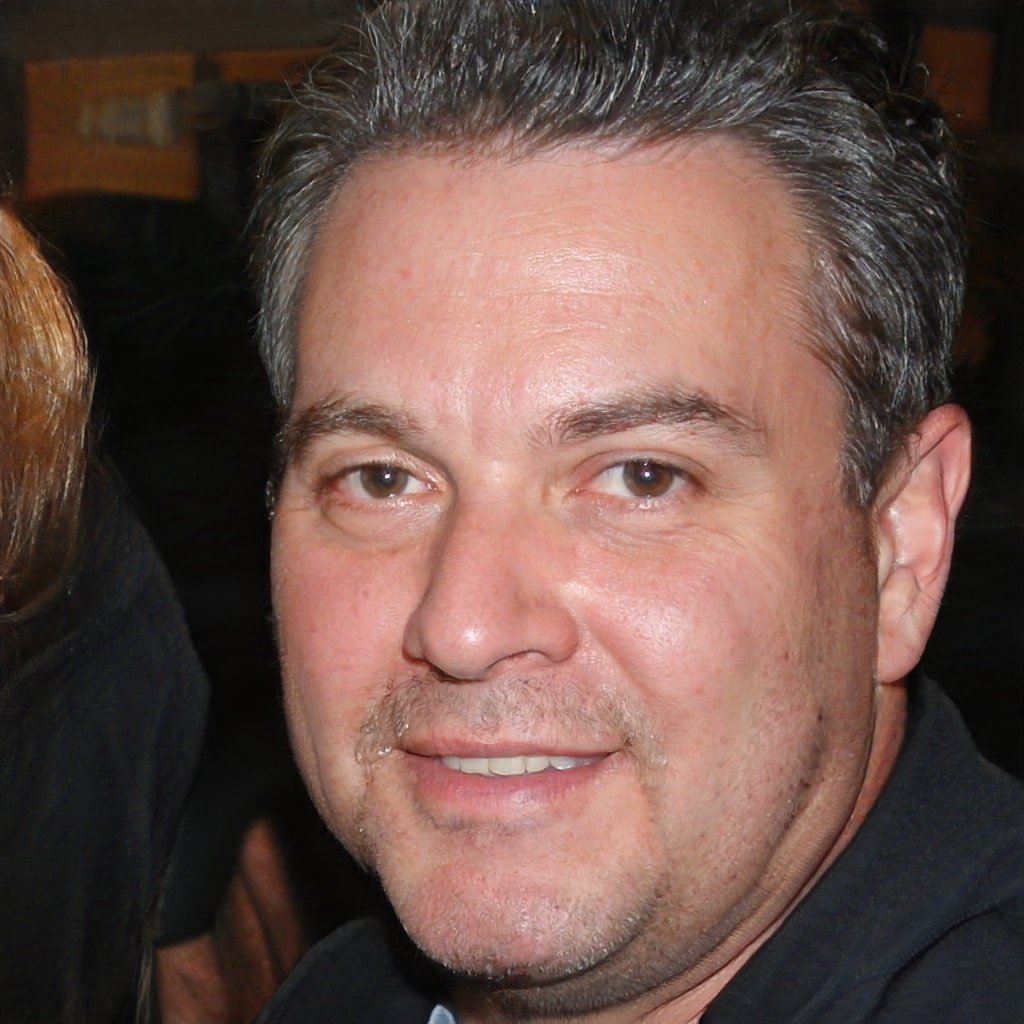